Applications of SMT Spring Finger Contacts
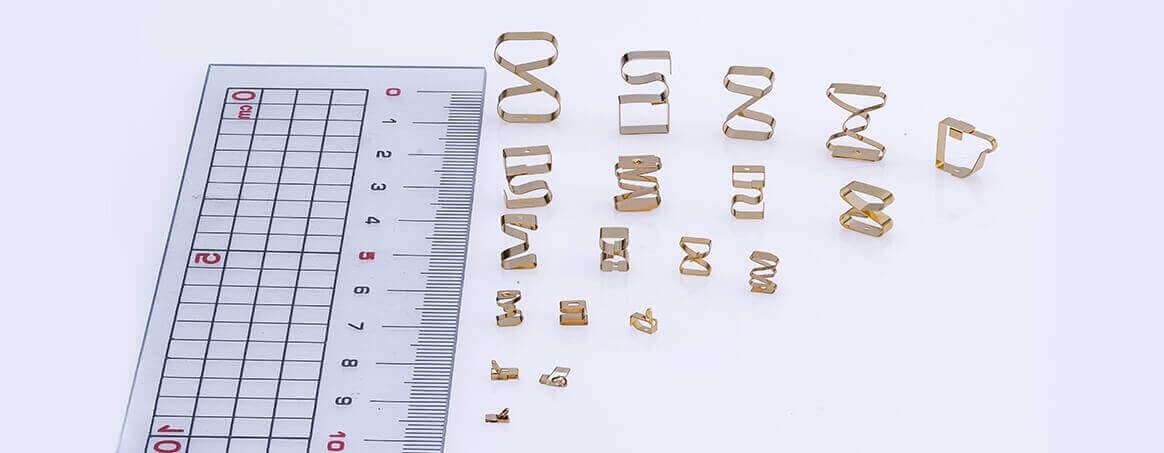
Applications of SMT Spring Finger Contacts
The production of SMT spring finger contacts starts with hundreds of meters of coiled metal strips as raw material with a thickness and a width pre-tailored in accordance with the design measurements. Among the metal materials, the most common one is beryllium copper. The production process involves placing the coiled metal strips on a payoff which feeds the strips inside a stamp machine where several tools are arranged in a circular fashion for various tasks such as stamping, cutting, bending to make spring finger contacts into desired forms. After the spring finger contact is completed, the next step is surface treatment. While the most economical coating is to apply nickel, it is recommended to have an additional layer of gold plating to enhance conductivity, humidity resistance and temperature resistance against harsh environments. After electroplating of spring finger contacts, the final step is tape and reel packaging so that they can be automatically assembled on printed circuit boards (PCBs). Overall, there are roughly seven processes to complete the production of SMT contacts.
Spring finger contacts come in various shapes with designated contact points that can be installed in all sorts of configurations to make vertical or horizontal contacts with the PCB. SMT contacts can withstand hundreds of thousands of compression cycles. In principle, it is not recommended to exceed 40% compression ratio of the contact height. For instance, a16mm high spring finger contact should not be compressed lower than 9.6mm in height. Excessive compression beyond the 40% ratio could cause permanent deformation of the spring fingers, which could lead to the loss of electrical contact.
The main material we use for making spring finger contacts is beryllium copper, which has limited thickness ranges and thus may not withstand high voltage or current. Depending on the SMT contact design, we recommend not to exceed 3A per piece for functionality despite sufficient contact thickness is required to cope with rapid and drastic changes in current or voltage. Given the contact weight, the requirements for automatic installation along with the constraint on maximum compression ratio not to exceed 40% of contact height, special contact specifications can be met by customization. For instance, for a larger compression ratio, thicker sheet metal might be utilized in making spring finger contacts. In such a scenario, elasticity of the SMT contacts might be compromised to a degree that the correlation between elasticity and compression ratio must be reevaluated and readjusted.
Spring finger contacts are widely used in the design of many PCBs with an extensive range of applications in automotive, medical, military, consumer electronics and many other industries. Finding the best-performing spring finger contact could be a challenge in preventing electromagnetic or radio frequency interference and static electricity. We have hundreds of standard spring finger contacts in stock that can provide our customers with immediate and cost-efficient solutions. Our professional design team with state-of-the-art expertise can also tackle any customization needs, from prototyping to mass production. If you have further questions or inquiries about spring finger contacts, please contact us at sales@oscarprecision.com